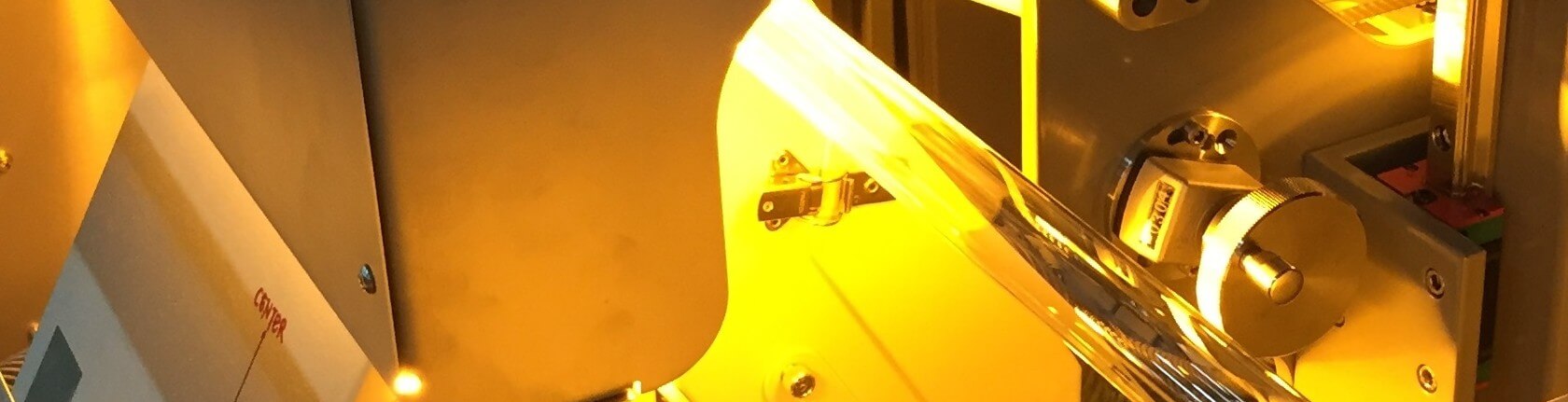
Clever Cutting for Glass Tubes
Reduce waste significantly with Clever Cutting
The production of glass tubes generates many faults and the only way to ensure the right quality is through sorting. This is a wasteful procedure, but Clever Cutting can help you improve the yield considerably.
Clever Cutting is an add-on to the JLI tube inspection vision system with the following features:
- Reduce waste by up to 40%
- Improve line efficiency with 2% or more - without any runtime costs
- Clever Cutting cuts only the defect section of the tube away
What do I gain?
With the introduction of Clever Cutting you can potentially achieve the following reduction in rejected tubes:
- Clever Cutting in 1/2: 25%
- Clever Cutting in 1/3: 33%
- Clever Cutting in 1/4: 37.5%
- Clever Cutting in 1/5: 40%
Based on experience the pay-back time will typically be 3-12 months depending on the current setup you have.
What do I need to get Clever Cutting?
In order to introduce Clever Cutting on your tubing line, you need the following:
- Inspection equipment able to point out the position of defects with good accuracy. Most current inspection equipment for Outside diameter and Wall thickness, Out-of-round and Siding can do this already and the defect inspection system in the SK-3000 series is able to detect the position of Stone/knots/inclusions and Airlines with high accuracy.
- Control software able to figure out which sections of the tube can form a full length of good tubing. Here the SK-3000 series systems play a vital role.
While OD, WT and other simple gauges just emit a digital signal whenever the readings are outside the tolerance, the decision on if multiple small knots or short airline are outside the tolerance is more complicated. Therefore, the only solution is to feed the digital reject signals from the OD, WT and other gauges into the SK-3000 series systems and then let this system decide which tubes to accept and which sections of tube to reject. - A cutter that is able to cut tubes in shorter sections controlled by digital signals. This can be achieved in several ways depending on the current equipment. If e.g. a rotary cutter in already in operation, it is possible to add additional cutting heads to the wheel.
Each cutter head will have to engage or disengage controlled by an electrical signal. With this approach, the wheel continues with the normal fixed speed, and the correct heads engaged to perform the necessary cuts are then controlled by a digital signal from the SK-3000 series system. If you have a cutter operated with a servo motor, the digital control signals from the SK-3000 series systems are fed into the servo motor controller and the cutter is activated at the correct time to cut at the right location. - A reject system that can handle rejected tubes of different lengths. This normally requires a minor modification to the reject mechanism itself and the lead-out of the rejected tubes, as the tubes now can be much shorter than normal.
- A conveyor for the accepted tubes that takes tubes that do not arrive with a fixed frequency. If the conveyor for accepted tubes is linked 100% to the cutter, so that the accepted tube falls directly into one distinct pocket, the reception area must be modified in order to make sure good tubes do not fall in between two pockets.
Most conveyors will work together with Clever Cutting without any modifications, and if modifications are necessary, they are fairly easy to perform.
What's the cost of Clever Cutting?
If you already have a newer system in the SK-3000 series (SK-3020, SK-3020D or SK-4020), you only need a software upgrade and commissioning to close 1) and 2) from the above.
The cost of 4) and 5) depends on what equipment you already have, but is normally not an issue. The unknown is the cutter. If you are able to modify your current cutting equipment, this may not be too complicated. It really depends on local conditions.
However, if you are going to replace the cutter anyway, it is obvious to make sure the new cutter supports Clever Cutting.
Technical description
Normally tube cutting is performed by a simple rotating cutter, geared to the pulling machine. Thereby, any defect detected will result in a full length of tube being discarded, no matter the size of the defect.
The principle of Clever Cutting is to cut away only the sections of the tube containing a defect, instead of throwing a full length tube away. Depending on the physical cutter, cutting the tube in half, one third, one quarter or even one fifth of a full length tube is possible.
If the cutter is a traditional wheel running with a fixed rotation speed, by adding additional cutting devices to the same wheel, users can obtain the Clever Cutting software from JLI to control the individual cutting devices.
This approach ensures that only shorter sections of the tube are rejected when defects are detected. The cutter can also be a single cutting device on a servo motor where the speed of the servo motor is controlled by the Clever Cutting software, so the time between two cuts matches the actual time needed just to cut away defective sections of the tube.
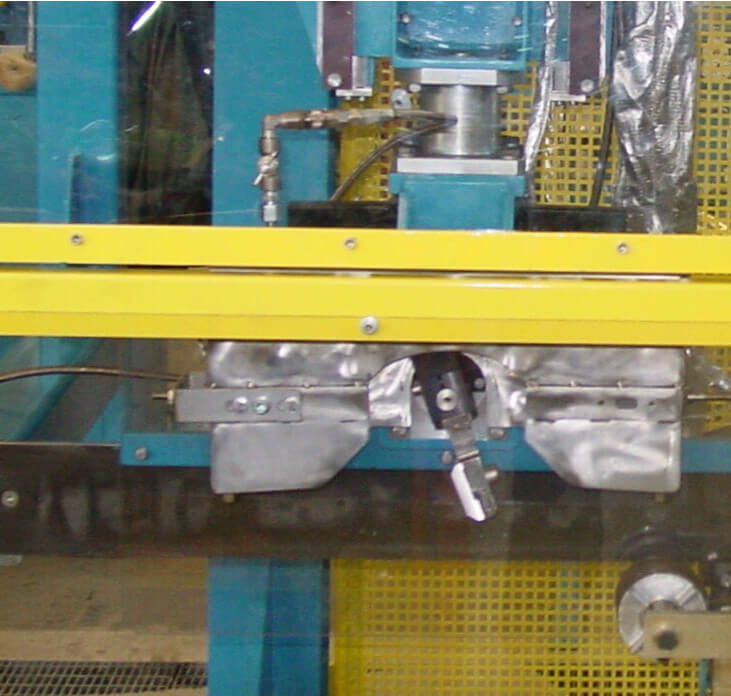
Why choose the JLI Clever Cutting System?
With the introduction of Clever Cutting you can potentially achieve the following reduction in rejected tubes:
- Clever Cutting in 1/2: 25%
- Clever Cutting in 1/3: 33%
- Clever Cutting in 1/4: 37.5%
- Clever Cutting in 1/5: 40%
Example systems in
Glass Inspection:
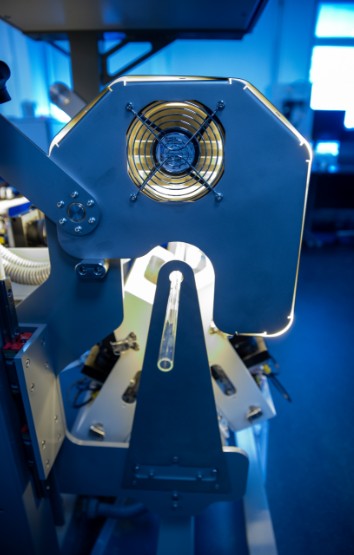
Designed and developed to meet high demands for speed and sensitivity.
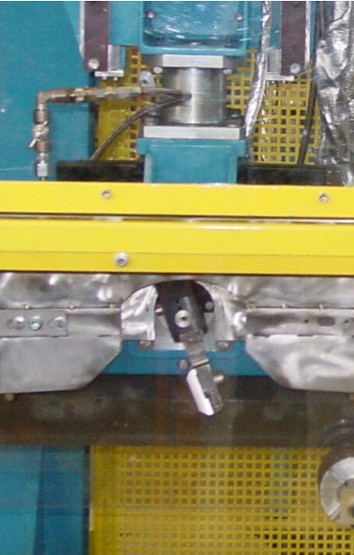
Reduce waste by up to 40%
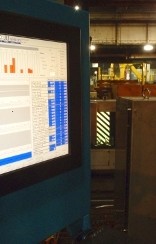
The system will continuously measure and inspect tableware as the glasses pass on a conveyor.
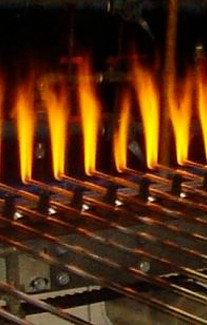
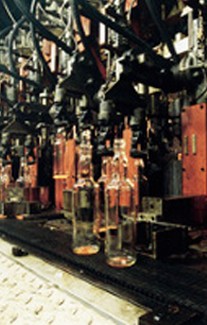
Book a meeting to learn more
.png)
Send me an email at hb@jlivision.com
or book a meeting, and let's find out how we can help you.
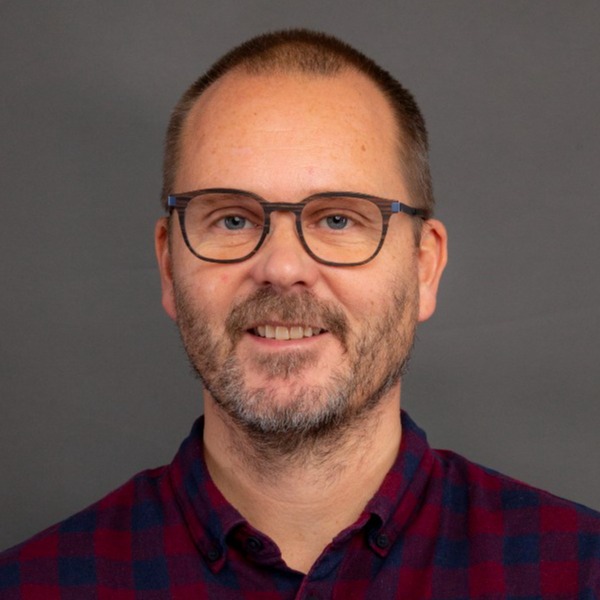