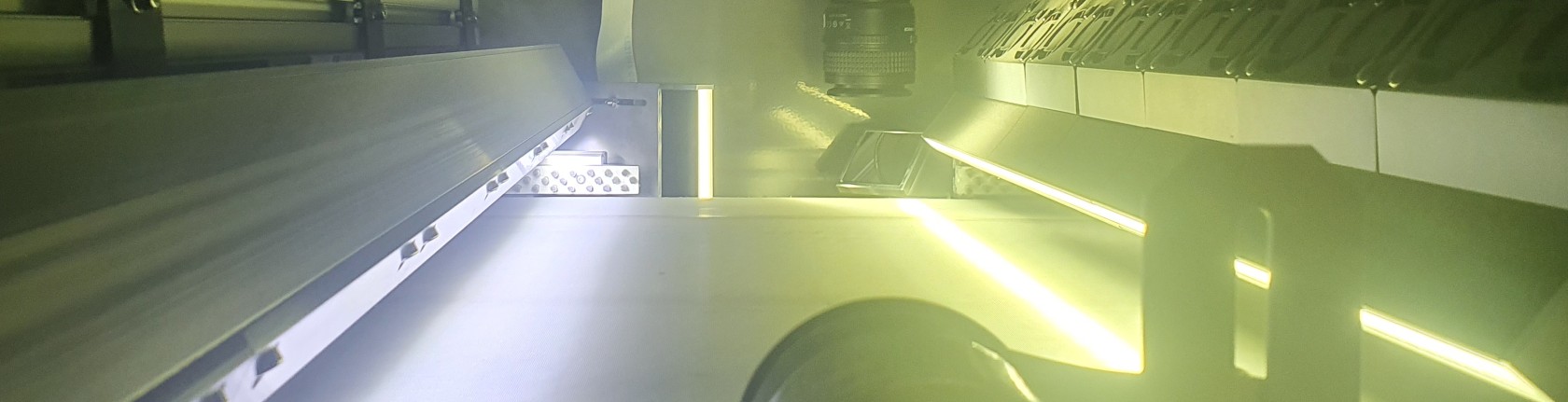
Inline Quality Control With Visual Non-Destructive Testing (NDT)
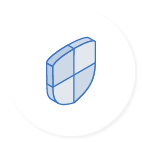
Visual Non-Destructive Testing (NDT)
Non-destructive testing (NDT) aims to perform quality control on products without damaging or altering the inspected material. At JLI vision, we create systems for visual testing on industrial production lines.
There are numerous NDT methods available, and which will be the right method to use is entirely dependent on the use case - the item or material to be inspected, and the kind of defects you will be looking for.
Here are some common NDT methods:
- Visual Testing (VT)
- Ultrasonic Testing (UT)
- Radiography Testing (RT)
- Eddy Current Testing (ET)
- Magnetic Particle Testing (MT)
- Acoustic Emission Testing (AE)
- Dye Penetrant Testing (PT)
- Leak testing (LT)
The most basic form of non-destructive testing is first on the list, visual testing (VT), and it is this type of NDT that we specialize in at JLI vision. We have created numerous solutions for non-destructive testing of steel products, for NDT in the wood industry, etc.
In many companies, visual testing is still done manually, but there are great benefits in automating visual testing by using advanced machine vision systems.
Fast and accurate inspection with automated visual testing
One of the benefits is maintaining a high degree of efficiency on the production line, as it is possible to set up machine vision systems to perform inline quality control as an integrated part of the production process.
In other words, you don't need a manual inspector to pick up the item to inspect it but can have the vision system perform a fast and accurate inspection of any surface defects you would be looking for and still maintain the flow of production.
Sometimes, you are looking for internal damages or defects, which is more tricky, as this requires the item to be disassembled for visual inspection.
With a robot sampling station, though, it is possible to have a robot pick up items from the production line, disassemble them, present the item to the machine vision system for visual testing, and then re-assemble the time and put it back on the conveyor belt. Traditionally this has also been a manual process, but by using a robot arm this can be done at high speed and with consistent accuracy.
Our process of creating NDT visual testing solutions
To create the right solution, we follow this process:
1. Project clarification
Analysing the specific challenges of your production line and the defects you wish to find to lay the ground for the right solution.
2. Collect samples
We will need a number of good and bad samples to start testing.
3. Create concept
Test phase to tailor the system to your needs.
4. Create the user requirements specification (URS)
The specific requirements for your solution can now be described.
5. Development and production
When the URS is accepted, we build your vision system.
6. Installation and training
We deploy the system at your factory facilities and train key staff members in operating the system.
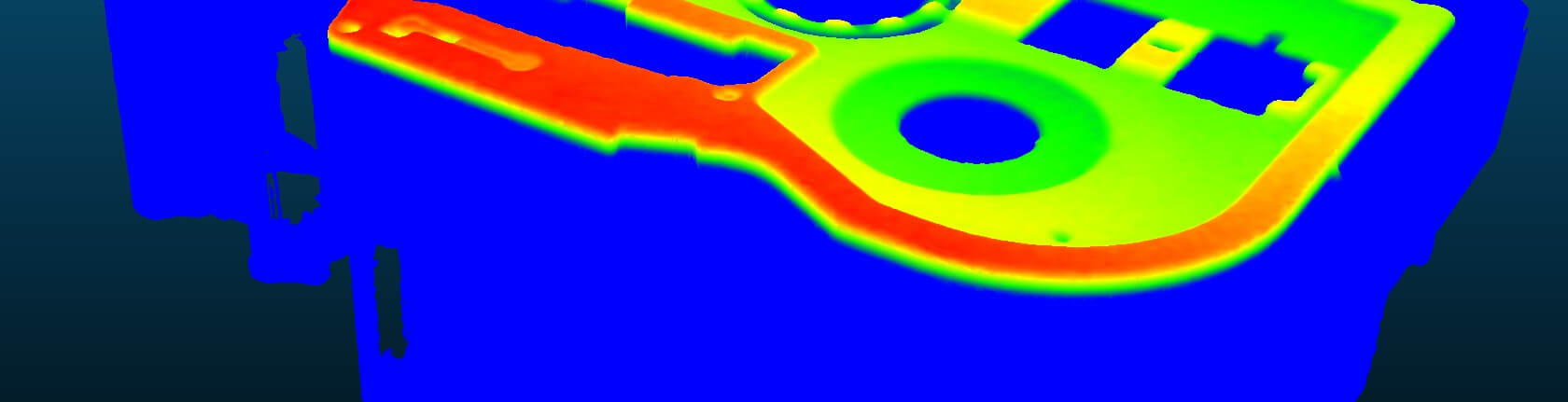
Why choose NDT (visual testing) from JLI vision?
- Custom-made systems to meet your needs
- Adapted to existing production lines to maintain optimal production flow
- High accuracy and consistent quality control
- Online access for remote support
Book a meeting to learn more
.png)
Send me an email at hb@jlivision.com
or book a meeting, and let's find out how we can help you.
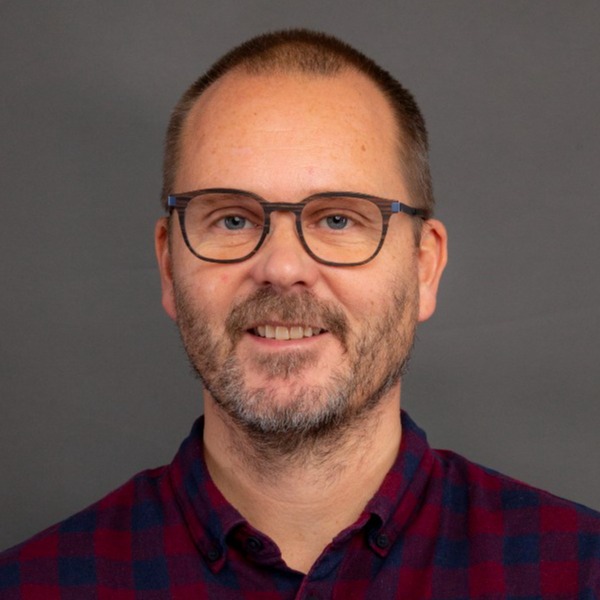