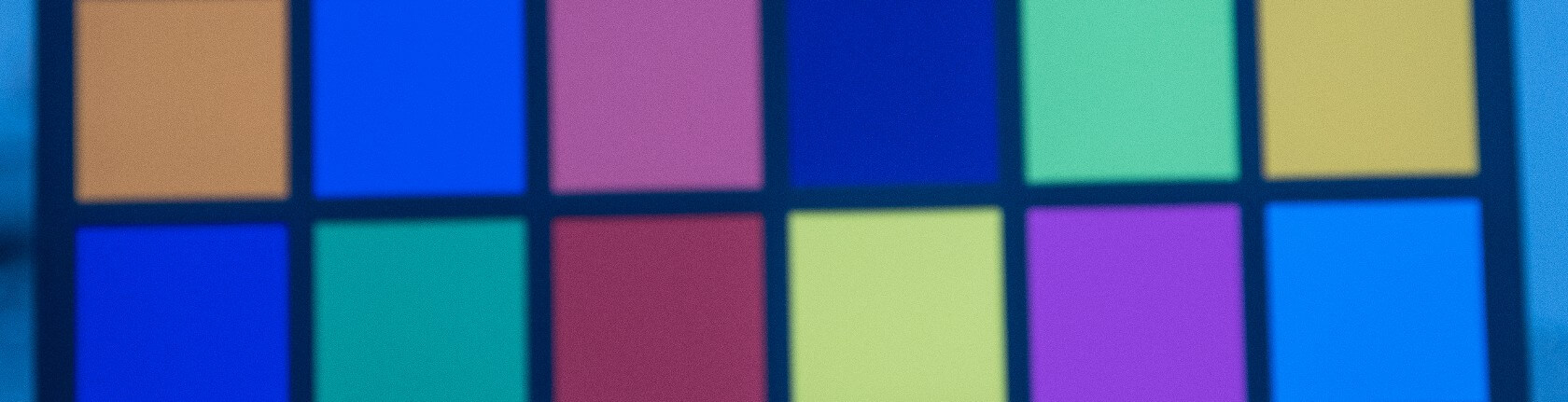
Color Inspection
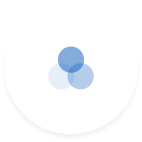
Achieving accurate color measurement
Identifying colors on packaging or other items might sound like a straightforward quality control task but color inspection is challenging and requires both expertise and experience.
Just like two people can have vastly different interpretations of the same shade in a painting or garment, in the field of machine vision, we face similar challenges in determining what color a color actually is.
The color inspection tasks we solve for our customers often have to do with identifying and separating colors as part of the quality control process. For instance, making sure that an item with a certain color isn't mixed with items of different colors during production or packing.
There are 3 main challenges we tackle in these projects to create robust color inspection system:
1. Avoiding reflections to measure the right light
A color is simply a reflection of a specific spectrum of wavelengths that is not absorbed by the material the light strikes. So to correctly identify colors you must make sure to measure the right light. The key here is to avoid direct reflection and instead position the camera in relation to the light source to measure a diffuse reflection.
We’ve tackled this specific challenge in a case with inspecting stacks of food packaging. The task was to ensure that the correct packaging was used in the production - based on the colors on the thin rim of the packaging.
However, the glossy surface meant that all the colors almost looked the same due to the color of the light from the light source becoming dominant.
Only by working with the positioning of the light source and camera in relation to the packaging it was possible to capture an image where the colors could be separated with high accuracy.
2. Calibrating the light source for accurate color inspection
No two light sources are the same, and this is important to remember if you want a successful color inspection.
If you need to change the light source in your machine vision system, you have to make sure that the system continues to detect colors in the same way as with the original light source.
This is done by calibrating the system with a calibration item - a color palette where each color has a predetermined value. By calibrating the system against these fixed colors, you can calculate correction factors that ensure the system measures colors in a consistent way, even if the light source is changed.
3. Choosing the right color space(s) to separate colors
In a machine vision color inspection solution, the colors are separated by mathematical values. The key here is to find the right color spaces to use for your calculations. Colors can be described in several ways with color spaces such as RGB, HSV, YCbCr, CMYK, and LAB.
Choosing the right color space or combination of color spaces is an important foundation for the calculations in the machine vision system. At JLI, we have developed a tool that makes it possible to quickly assess how close the colors are to each other in the different color spaces and thus assess how easy or difficult it will be to separate them with a machine vision system.
A deep understanding of color inspection
At JLI, we have a deep understanding of color, light, and the nuances of accurate color measurement.
We have developed a series of calibration tools that provide precise color detection and have helped our international customers maintain consistent control over their colored products throughout the production process, from supplier to final product.
Read more about color inspection here: How to find the best method for color inspection
Book a meeting to learn more
.png)
Send me an email at hb@jlivision.com
or book a meeting, and let's find out how we can help you.
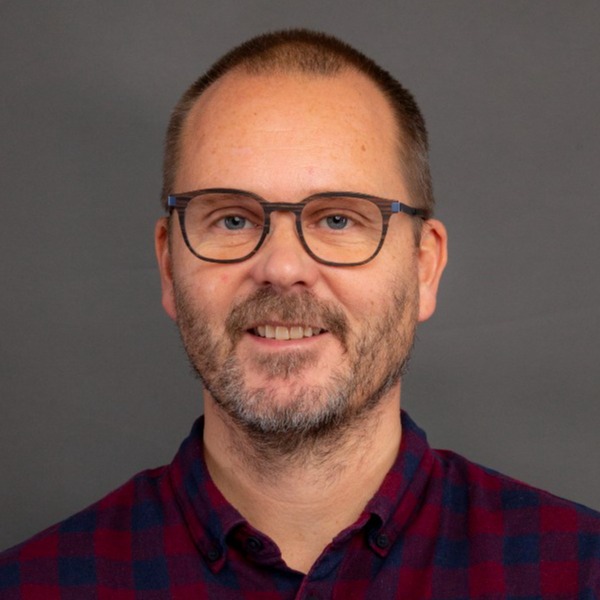