Zeeland Pharma
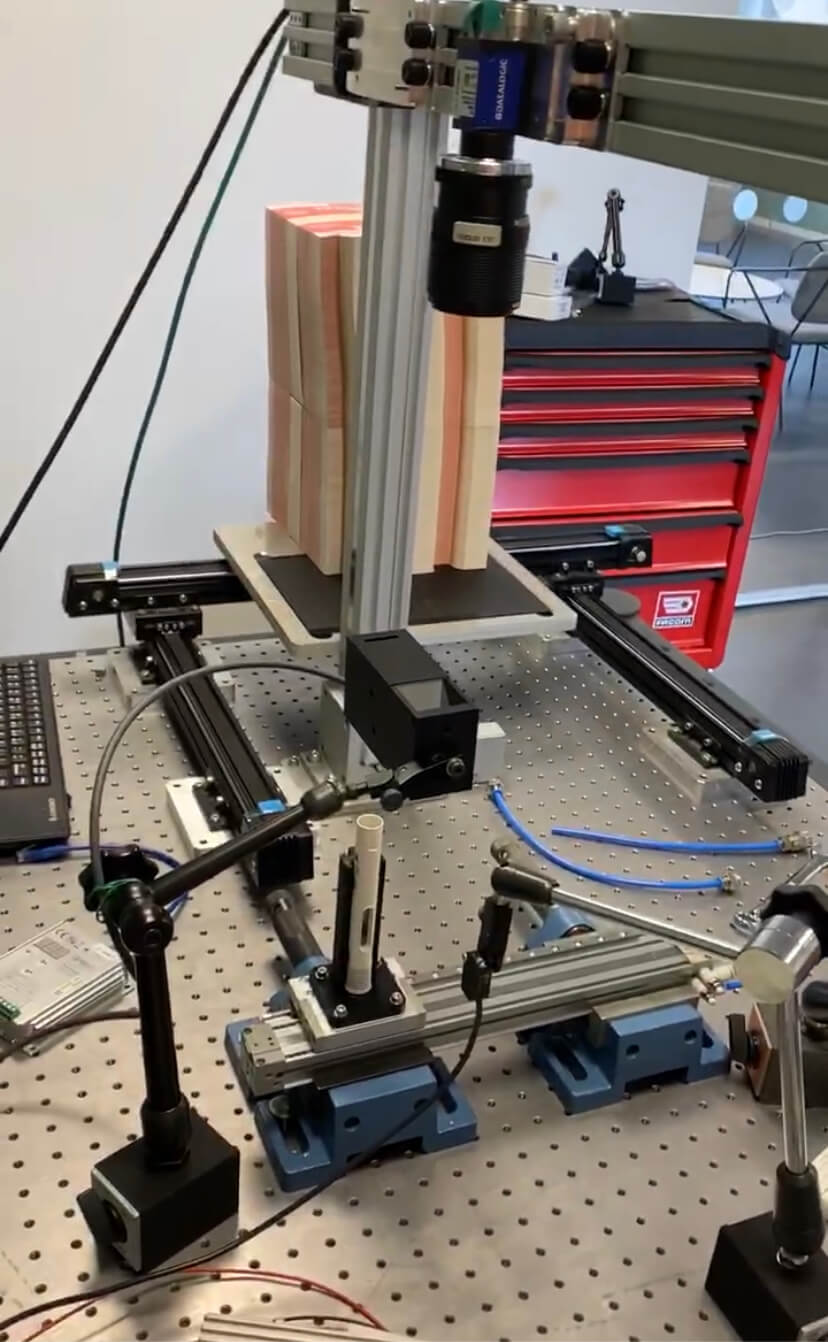
Automating a complex inspection task on a strict time limit
“How can we automate a tedious and difficult manual inspection and ensure the safety and quality in the production?”
This was what Zealand Pharma was looking for when they contacted JLI vision.
Zealand Pharma recently developed a new product and had just commissioned a new machine to produce the first units. Now they wanted to automate some of the manual inspections while keeping high quality and safety standards for their products.
JLI vision has developed and produced inspection systems for medical devices since 1986, and therefore JLI seemed to be an obvious choice.
Zealand Pharma had three very strict requirements:
The system should perform the inspection with 99,9 % accuracy, be ready in just 3 months, and it had to fit into the existing machine. This machine was not designed with machine vision in mind.
JLI vision made a replica of the machine setup
To find the right solution for the vision inspections, it was important to know the physical constraints of the production machine.
It was found, that it was only possible to fit the vision inspection in a part of the machine where the devices were moving at speeds of approximately 200 mm/s.
This had the consequence, that the shutter speed of the camera should be quite fast to avoid motion blur. Some motion blur is acceptable, but it complicates the image processing and reduces the sensitivity of the system.
When shortening the exposure time, the demand for light intensity increases. In this case, the demand for illumination was high. To find the correct combination of camera, lens, light, and timing, JLI vision made a replica of the machine setup, in their laboratory.
After some experimentation, this resulted in a setup where a sensor would trigger the camera and light source, at just the right time to get a picture. The engineers at JLI vision were confident that this would provide enough information to categorize the devices as either accepted or rejected.
Zealand Pharma also found, that one of the cylindrical parts in the devices could potentially have a break in its molding. It was important to know before it assembled with other parts in the machine.
The defects were not in a fixed position so pictures spanning the part’s entire circumference were needed to catch breaks.
To solve this, JLI vision developed a small box with a motor to rotate the part while light and camera were triggering at a high rate.
This solution ensured pictures from every angle. The pictures were then analyzed to determine if the part was fit for installation in the device.
The system achieved the required accuracy of 99,9%
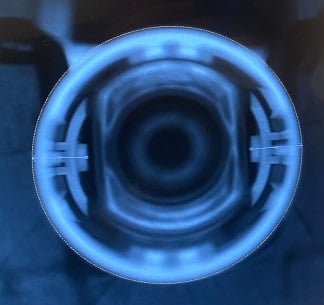
The system lives up to strict requirements
After passing the factory acceptance test, the system was commissioned into the existing machine.
Cameras and light sources were adjusted to fit the production environment.
During site acceptance test, it was confirmed that the system, among other requirements, lived up to the strict demands of an accuracy of 99.9%.
According to Zealand Pharma’s Head of Device Development Lars Stenholt, the cooperation with JLI vision has been very good and flexible throughout the project.
He also adds that JLI vision’s input and knowledge helped to evolve the system into what it is today.
Zealand Pharma and its suppliers do not expect to produce faulty products and are very careful that the production is performed correctly and safely.
Since the vision system was implemented, it has detected very few defects among the many inspected devices. This both shows the quality of the production, but also that if the slightest non-regularity happens, the vision system is ready to detect it.
.jpg?width=1440&height=696&name=Group%2050%20(1).jpg)
Download the case study
Can we help you, too?
.png)
Send me an email at hb@jlivision.com
or book a meeting, and let's find out how we can help you.
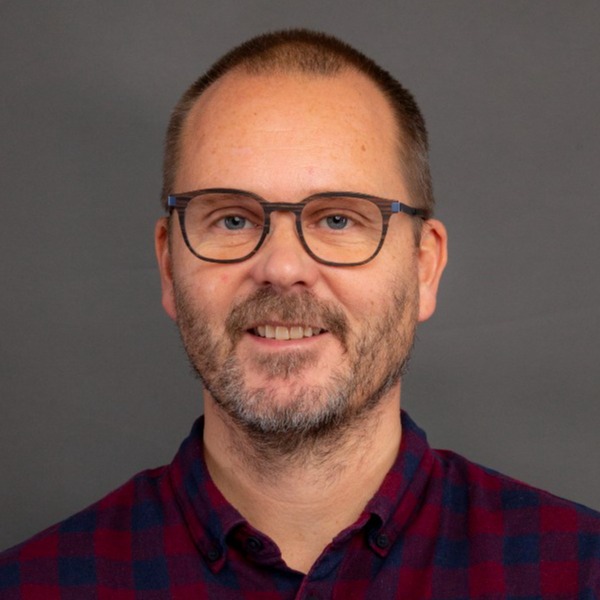