Vision systems can be used in quality control or for optical measurement. They can be used to speed up processes or reduce man hours spend in the production.
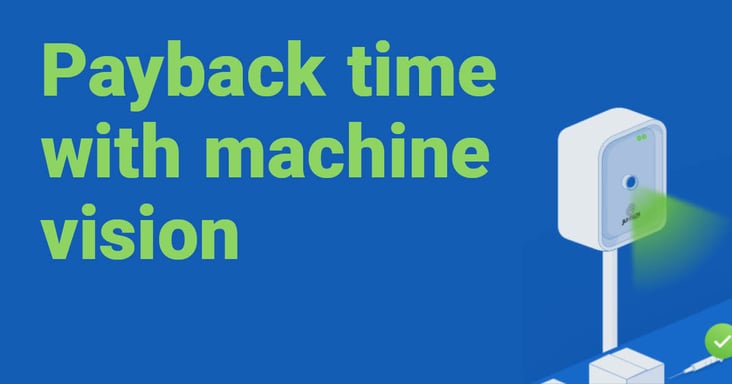
30 years ago in 1989 JLI installed a vision system in a UK steelworks.
This is a good example of a system for a harsh environment and with a very fast payback time.
The steelworks produce very expensive titanium steel used in exotic applications like helicopter hubs, turbines in jet engines and even in the Space Shuttle.
The ingots or concast blooms are rolled into billets. After rolling the nose and tail is cut and discarded. As the material cannot be reused it is important to cut precisely. If you cut too little you do not get the impurities removed from the ingots and if you cut too much you waste material.
This job was done by an operator who looked at the billet ends and positioned them under the cropper by joy stick motor control of the roller table. The distance from the cropper to the pulpit was 15 meters. Each end was cut depending of the material and the length of the billet. The cut lengths were done by eye. The precision was not overwhelming and there was a tendency to cut too much off.
When we got the order there was a great pressure on us to get the system in operation. When it was commissioned we all went to the local pub and celebrated. It was there I understood the eager to get the system operational.
The steelworks had calculated that the loss due to excessive cropping probably was about 1.5 %. As the steelworks had an annual production worth 13 million £ this loss was about 200,000 £ pr. year. The cost of our system was 32,000 £ giving a payback time of only 2 month months !
After 18 yeas of flawless operation a new system was installed. It was decided as the parts for the old system were no longer available and the risk of a breakdown that would disrupt production was too high. The new system did exactly the same as the old system but was designed to allow for new features.
The latest development is to make the vision system control the roller table and position the blooms automatically. This should achieve an even more consistent cropping and save man hours. As the steelworks operates day and night this is a substantial saving.
Below is a typical screen where the aim line is in yellow and the detected end position is in red.
The system has identified the end of the bloom as a fish tail, and will position according to the cut off required. If a git end is detected the cut of is different.
This system is an example of precise measurements in a harsh environment. It shows that mm precision can be achieved, and that the whole process can be automated.
It is also an example of the great savings and a fantastic payback time of only two months!
You can learn more about how machine vision can increase your earnings by following this link.