Machine vision is an automated inspection system installed directly at the conveyor. It will inspect the products, reject defects and gather statistical data.The increased need for higher productivity and better quality in manufacturing demands a more effective and streamlined quality control.
The Machine vision systems can be used in various industries and processes and it helps you solve inspection tasks that is either to difficult or time-consuming to do with manual workforce.
You will find Machine vision everywhere, even in your smartphone where face recognition and other features are becoming standard.
Introducing Machine vision
The first industrial vision systems appeared in the mid-eighties. They were big and slow but could solve many industrial inspection jobs.
Since then everything has become smaller, faster and better as the hardware developed. The software has had great breakthroughs, latest by the introduction of artificial intelligence and Machine Learning.
Basically, the vision system applies the right illumination, takes the picture and transfer it to the memory in the computer. Then the program starts to work.
You can learn more about machine vision in this introduction guide
Machine vision hardly ever compare pictures pixel by pixel, this is not the way they work. This would require very precise alignment, like in a printing press. What you do is to take measurements in the picture and compare them to measurements from a master image. It is the measurements, - distance between points, angles and intensity - that goes into the inspection algorithms. When the measurements are within tolerances the part is accepted. If not, a reject is generated or statistical data is generated.
To take an example, the picture format may have a pixel count of 1.000 by 1.000. However, this is not the limiting factor. If you have a picture field of 1 meter by 1 meter thereby giving a pixel size of 1 mm, you may think that this is the accuracy. It is not.
Integration techniques can improve the resolution up to a factor 500, meaning that in a 1-meter picture, you can measure with 2μm accuracy. This requires a lot of work on compensations and calibrations.
Integration techniques are used in almost all the vision systems we develop, not necessarily to increase accuracy, but more to improve reliability. Never trust one pixel! – use all the pixels you can to make the system robust.
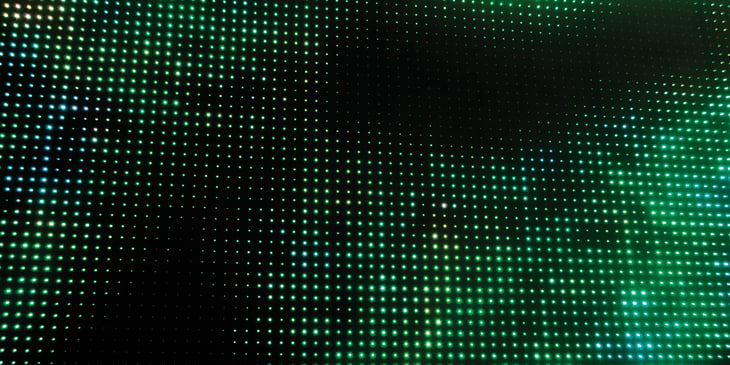
Another feature in vision systems is the contactless gauging. You can place the cameras far away from the process you want to monitor.
This is really useful in harsh environments like in steelworks. Some systems measure red hot steel from a distance of 25 meters.
Vision systems have developed a lot since their introduction 30 years ago.
The first systems were expensive, big, slow and not very user friendly. They required a lot of specialist programming and were sensitive to changes in inspection conditions.
Many of the jobs we automated 30 years ago can now be done with smart cameras. These are small easy to use devices, and they can be programmed in a high-level language. You do not need to be a Machine vision expert.
One important part of a vision system is the scene, the illumination and the optics. It is important that the parts you want to inspect are presented in the right distance and angle, and that the surface of the
part to be inspected does not change too much.
This part of the vision solution is still the same. Without a good image you will never get a reliable performance.
Working with the scene, light and optics is something that require special skills. It is the expertise you gain from developing many different solutions in many different industries.This was a short introduction to the Machine vision technology.
If you want to learn more, you can download this introduction guide to Machine vision.